brainwagon (reborn)
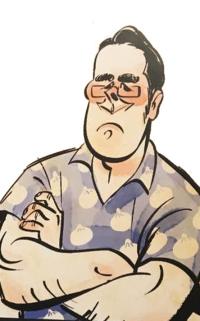
Welcome to the brainwagon blog, the online site of Mark VandeWettering. I have been blogging about random detritus in my life for over two decades using Wordpress, but recently decided that its complexity and features no longer were a significant benefit to me. So, like the Beverly Hillbillies, I packed up all my stuff and decided to move.
This site is generated using a modified version of Sunaina Pai's makesite.py Python script. My modified versio generates this blog from Markdown source using under 500 lines of very comfortable Python. It doesn't include things like extensive documentation, theming or the like because the code is so simple that if you have even the most rudimentary Python experience, you should be able to read the code to see how it works. (You can expect a link to a github repository as I tidy it up for release to the public)
I have exported the 4300+ posts from the older Wordpress and the text of all the posts that were previously hosted at brainwagon.org are now visible here. There are a few caveats that I'll be working on over the next couple of weeks. My goal is eventually to move the blog entirely off of Wordpress.
I have also made an endeavor to try to do as little styling as possible, consistent with making something that looks a little better than just the naked html. I'm debating whether leaving all font and sizing should be left to the user in that regard, and am trying to work toward that ideal.
There are a number of things which are not quite in place yet.
- While the text of every post is expected to be intact, references to other resources like images or downloadable files are almost certainly broken. Some images will work by referencing there current places on the current brainwagon website. I am working on automatically updating them all to refer to a static subdirectory that will contain them, but it might take some time to update the 1300+ image links to make sure they work. To be fair, about 270 or those links (mostly made before 2012 or so) are broken as they seem to have been lost in some backup/restore fiasco several years ago. I am working to use the Internet Wayback machine, and should be able to get the majority of those.
- User comments are not yet injected. I have not seriously looked through the exported data to see how it might be possible to add them to the archive. Going forward, the blog does not support user accounts and commenting, although I have been interested in seeing whether something like Disqus, Webmention or ActivityPub could be integrated into this simple system without undue headaches. Stay tuned.
- The default makesite.py script does generate RSS feeds, but I think that at best this is a tremendously niche way of people to stay informed. I want to create some gatewaying between my Mastodon accounts and this blog. Longer format posts will continue to be hosted there, with mastodon.social/@brainwagon being used for more short form thoughts and updates.
- I do find that I refer back to my blog often for things that I may have written about in the past, and thus I find that a reasonable search capability is desireable. I chose pagefind to be a reasonable solution, which can accept an entire website and performs indexing that can injected and done entirely on the web client. I am still experimenting, but for now that is the search solution that I have settled upon.
In any case, if you are reading this and have any comments or questions, feel free to send me an email and I'll try to respond. My goal is to eventually write up a more complete HOWTO on how I created this.